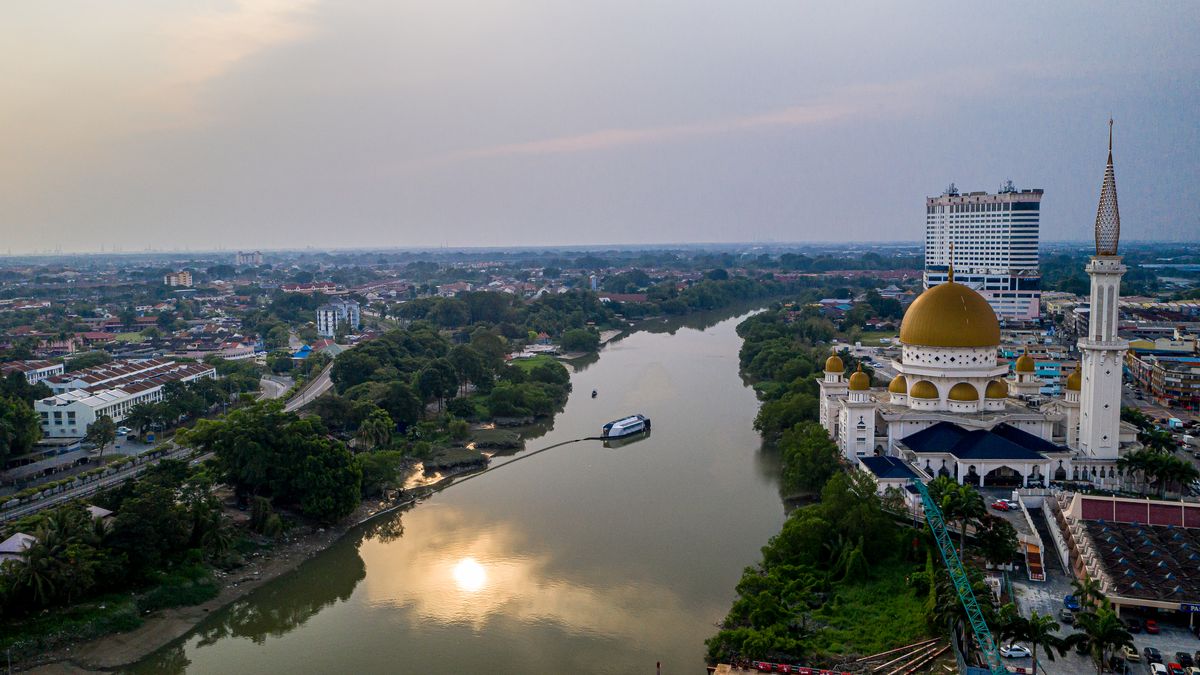
By mid-2018, after digesting all the lessons learned from the testing phase of Interceptor™ 1.0 in Zuidland and taking into account all the findings from our river research, our engineers started designing a new concept and basic design for our second Interceptor ™ 2.0.
The many lessons learned from Interceptor™ 1.0 required a new approach in the design of Interceptor™ 2.0. Along with our design partner TME, changes were made to focus on capacity and operational cost. The biggest of these changes were replacing the big bags used for storing debris with containers, which eliminated the carousel element used for distributing the debris to the bags. Instead, a shuttle conveyor was designed to distribute the catch over all the containers. We also enlarged the capacity of the system to enable more debris to be extracted, the conveyor belt was made 1.5 times bigger, and the storage capacity increased six-fold. Other changes included: improving hydrodynamics and stability and locking mooring resistance to ensure the system remained in the correct position at all times.
Similarly to our ocean cleanup design, we believe simplicity is key for operations and mass production. At this point, we knew we were aiming for a design suited for series production, that could be utilized in rivers and countries all over the world, we made these changes with a focus on improving the general ease of use and cost of operations.
Case studies were performed in 2018/19 at river sites in Vietnam, Indonesia, and Malaysia to gather information for the basis of design and deployment of the Interceptor™ 2.0. Using the minimal capacity requirements from the results of the studies, we could project the required number of extractors needed to achieve our goal. The deployment of these systems and of Interceptor™ 1.0 will provide extensive knowledge of how riverine plastic can be extracted most efficiently, what challenges we could expect in this operation, and how the system could be monitored and actuated for automatic operation.
In November 2018, our partner TME started building the new system in Kampen, near Zwolle. The assembly of the system would take place at the testing site and then installed. In the Netherlands, the test site chosen was Hedel, in Gelderland. In January 2019 the assembly started and finished in May after which testing started. In July our whole team had the opportunity to visit the Hedel site to experience the full impact of the Interceptor™ 2.0 in situ.
While the team was viewing the Interceptor 004 in the Netherlands, assembly commenced for our soon-to-be-deployed Interceptor in Malaysia. After conducting our case studies and working together with the government and local partner, Landasan Lumayan Sdn. Bhd. (LLSB), we were ready to install in the Klang River. Assembly finished later in August and was towed to its deployment location on August 15; making this the second Interceptor to be fully operational in the world, kickstarting the roll-out, and helping us to prevent more plastic from entering the oceans.